1. SE(Simultaneous Engineering)
お客様が要望する製品データを事前に入手・検証し、金型として成り立つかどうかを調査します。その調査結果をもとに、製品形状の改善や変更をお客様に提案します。製品の設計段階からお客様と共同で取り組むことで、お客様の製品設計に要する時間や設計変更回数を削減します。
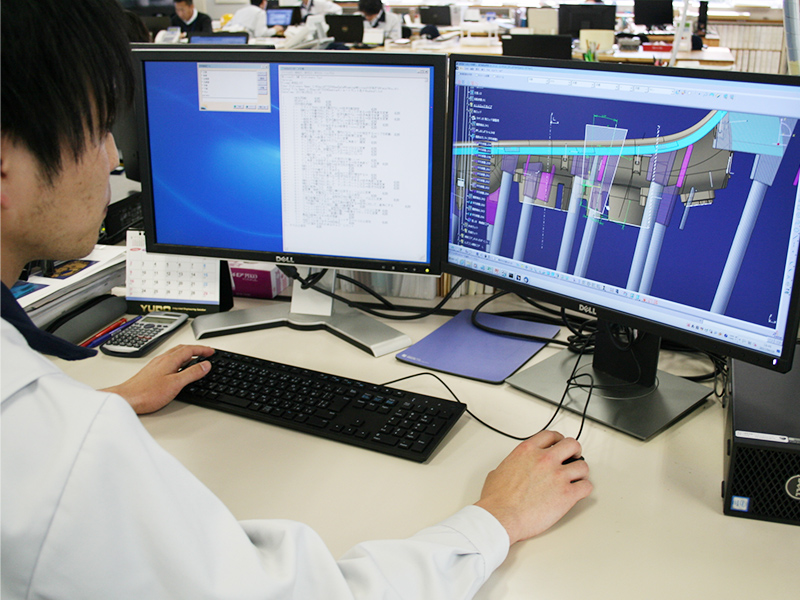
2. CAE(Computer Aided Engineering)
樹脂の流動解析を実施し、成形時間を最適にするためのゲート位置やヒートスポット部位に対する水冷回路を検討します。成形機ランクを検討し、その結果をもとに最適な金型構造をお客様に提案します。
近年は、樹脂材料の特性を実測し、そのデータを使用することで解析精度をより高める取り組みを行っています。
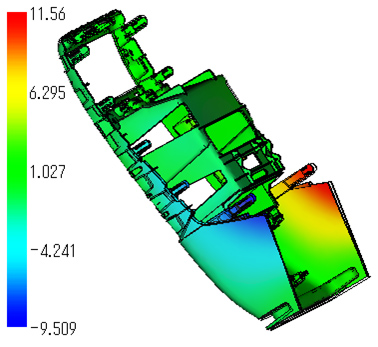
3. DR(Design Review)
金型の構想設計が完了すると、製作に携わる全部署が集まり、金型製作に関するコンセプトや新たな取り組み内容などを検討し、情報共有・意思統一を図ります。
さらに、過去に製作した類似製品で発生した不具合を調査し、未然に防止するための対策を立案します。これにより、短納期・高品質を満たす金型製作への第一歩を踏み出します。
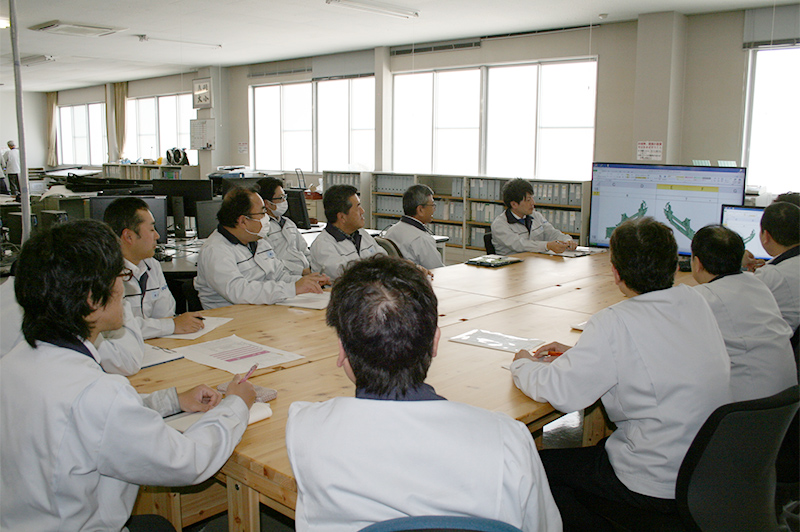
4. 金型設計
金型の品質の70%は設計段階で決まると言っても過言ではありません。
お客様と検討した製品データをもとに、最適な加工、最適な組付けを考慮しつつ、三次元金型設計システムと当社独自のマクロ(プログラム)を活用し、自働設計を進めます。
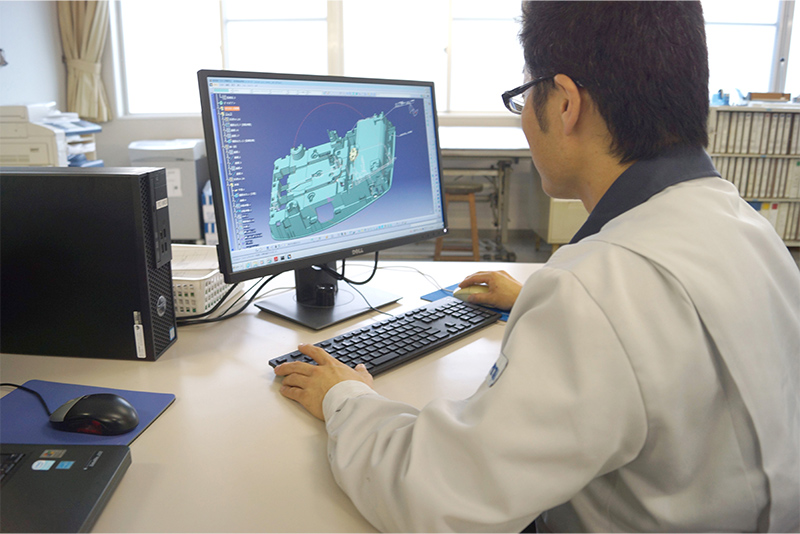
5. CAM(Computer Aided Manufacturin)
設計された金型のデータをもとに、それを実際に削るための加工データを作成します。
いかにして速く、精度よく削ることができるかを永遠のテーマに、常に新しい工具、新しい加工方法に挑戦し、レベルアップしつづける工程です。
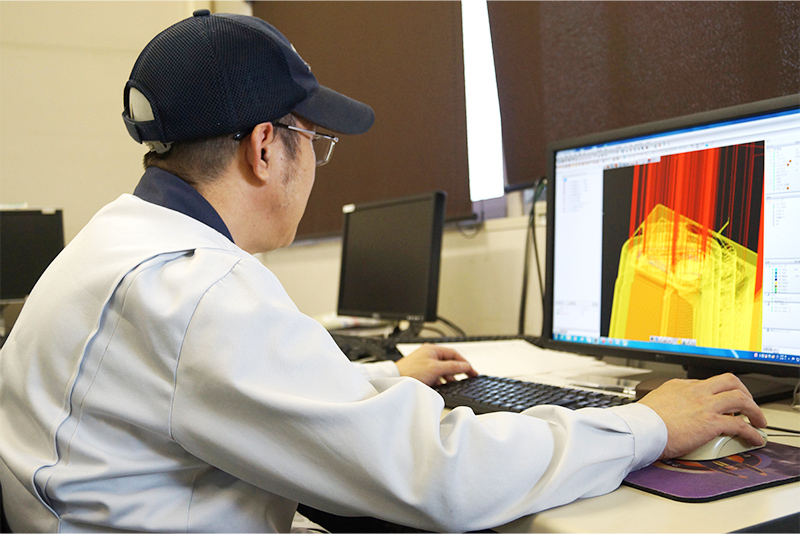
6. 機械加工
金型の大きさが2mを超える大型から小型精密型まで、あらゆる加工ができる設備を使いこなし、要求された品質・精度を満たす加工を行います。
現在は、段取り回数を極限まで少なくするワンチャッキング(一度セットするだけですべての加工を完結させる)活動を行い、5軸加工機による金型部品自動切削ラインにて、さらなる速さ・精度の向上と工程間ロスの低減に取り組んでいます。
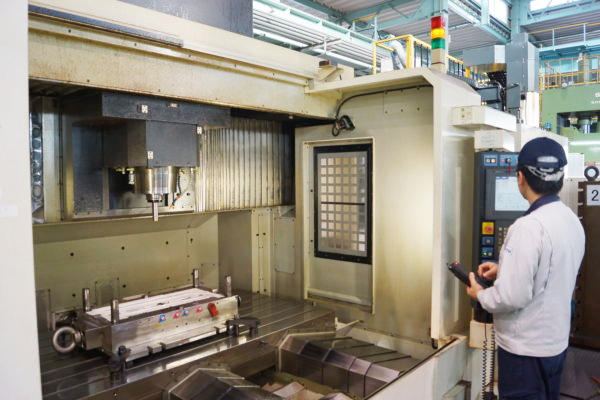
7. 放電加工
刃具切削では加工できない形状を加工するための工程です。電極と呼ばれる凸形状を作製し、その電極に電流を流しスパークさせることにより鉄を溶かし、目的とする形状加工を行います。
こちらも速さと品質両面を満たすために、材料別による加工条件などを日々追求しています。
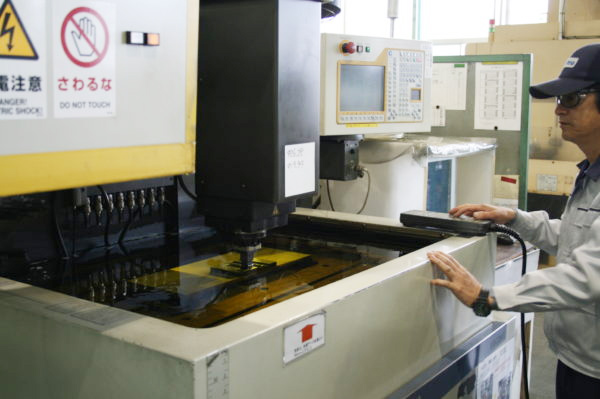
8. 組立て、仕上げ
金型は数百点の部品から成り立っています。それらすべてを正確に組み付け、スムーズに動くように調整する最終工程です。腕によりをかけて一品料理をつくるように、高い技術・技能を持った社員たちの手で金型は完成されていきます。
また、メッキ製品などに用いる金型は、製品面の面精度、面粗度が重要となるため、ここでも「ミガキ」 に対する職人気質を持つ社員が高い技能を発揮します。
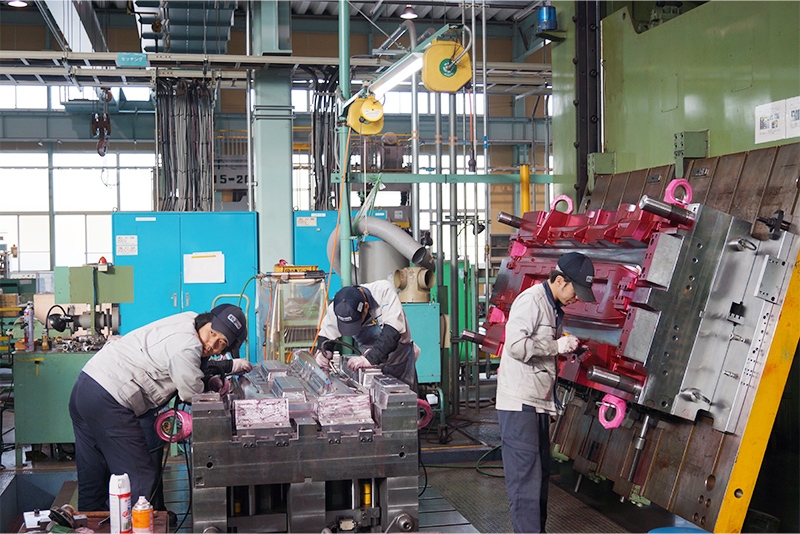
9. ASSY測定
部品単品としての要求精度はそれぞれの工程で保証されますが、金型に組み付けられた状態での精度保証も必要です。
寸法管理が必要な部位については接触式三次元測定器を使い、数値にて精度を保証します。
また、製品面のうねり具合など、全体の測定は非接触式三次元測定器を使い、カラーマップなどのイメージにて精度を測定、保証します。接触式、非接触式の二つの測定器を駆使し、お客様にご満足いただける金型をつくります。
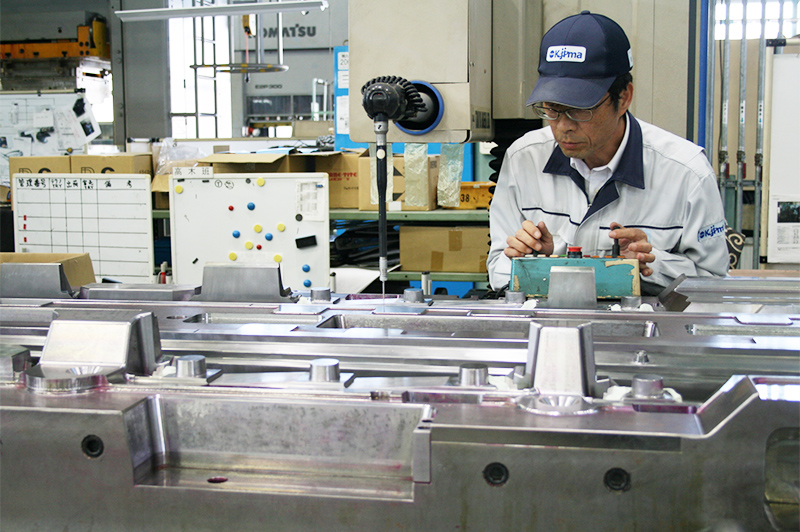
10. 成形トライ
お客様が望むのは金型の出来栄えではなく、金型を使ってできる製品の出来栄えです。その確認を行うのがこの工程です。
お客様にご満足いただける製品となるよう、小型から大型まですべての金型用成形機を備えて成形された製品の外観、寸法などを確認します。そして、実車に取り付けた状態を再現し、取り付け位置、相手形状とのスキの確認などを行います。
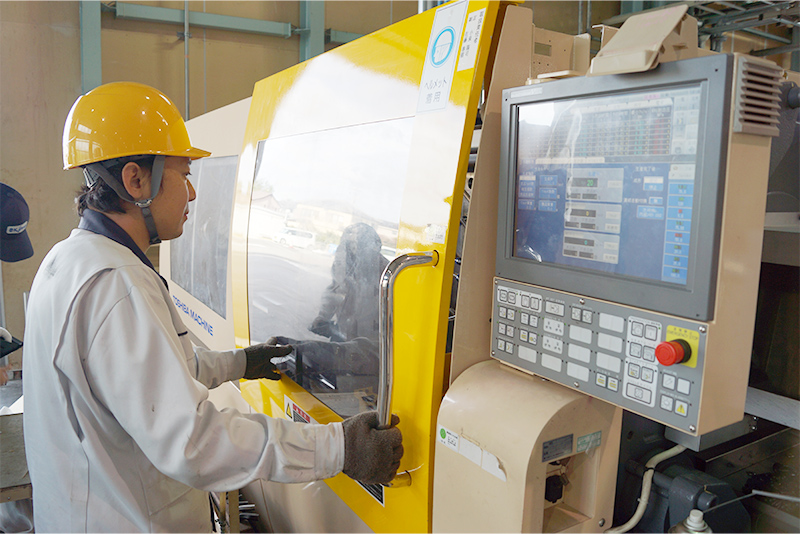